Machining Function
Contour Face Cut Machining / High-feed Machining
The exclusive cutter paths are generated and output for “High-feed Machining” with utilizing the characteristics of the high feed milling cutter.
Machining time is reduced with the best cutter paths.
Comparison
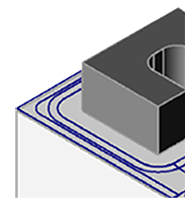
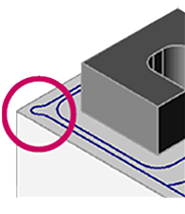
Modified tool path is output to pass through the uncut portions. Pick width in XY direction is also adjusted.
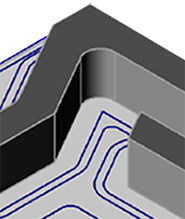
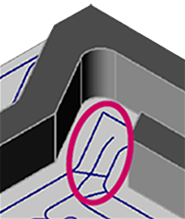
Forward and reverse tool path that passes through the center of uncut portions is output.
Add of Pseudo R Function
Outputs the tool path by adding R-shape corners to the concave angle portions of the machining geometry.
Reduces the load of tools when using the tools in R corners and deep grooves for rough machining. Also, users can omit the addition of R-shape corners during modeling.
Image of Pseudo R Addition
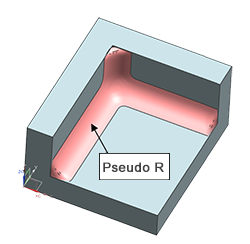
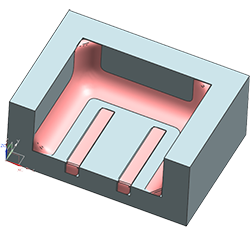
Examples of Tool Path Outputs (Corner R Portions)
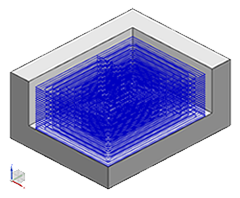
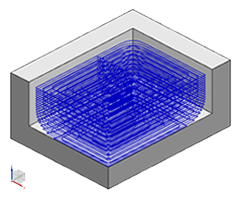
Add of the Model Vertex Auto Recognition Function
Automatically recognizes the machining geometry vertices and adds the tool path of rough contour machining to its Z level.
Reduces the uncut portions between contour steps at the machining geometry vertices to prevent holder interference.
This function can be used for “Contour Rough Machining”, “Contour Semi-Finish Machining”, and “Contour Finish Machining”.
Normal Contour Machining
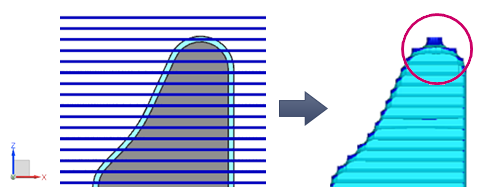
Contour Machining Using [Model Vertex Auto Recognition] Function
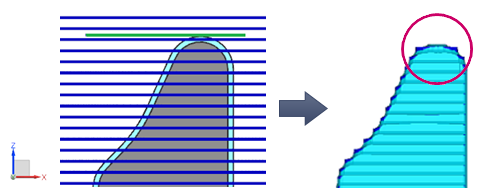
Simulation
Add of New Functions to CSG Data Output Function
It corresponds to Professional 6 (Pro 6).
Professional 6 : Advanced control device designed to maximize mechanical performance.