FFCAM 2017 New Function
Machining time is reduced with the best cutter paths.
Machining Functions
Machining Direction Calculation
When the target surface for machining becomes selected, the best “Machining Direction” and “Overhang Length” are computed automatically. The time to be considered a machining becomes reduced drastically.
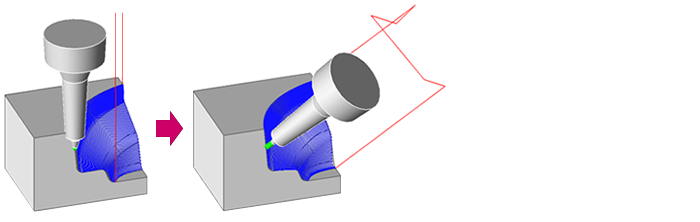
Index Angle | Overhang length | Machining Consideration Time | |
---|---|---|---|
Mr.A | A-axis : 68 , C-axis : 12.5 | 27mm | 40min. |
Mr.B | A-axis : 53 , C-axis : 20.0 | 30mm | 15min. |
Mr.C | A-axis : 50 , C-axis : 15.0 | 30mm | 30min. |
Machining Direction Calculation | A-axis : 63 , C-axis : 12.0 | 30mm | 5sec. |
Consideration time by this shape About 90% reduction!
Added the Function for Using Multi-Edged Tool
By specifying the [Feed speed] according to the tool and work contact surface, the feed speed can be increased when machining with the tool side which consists of many edges. The [Feed speed] is automatically inserted into the NC program,reduce the burden on CAM operator.
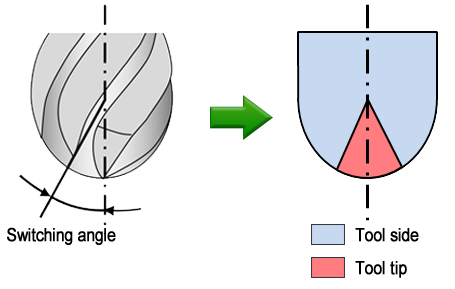
When “Number of blades = 4”
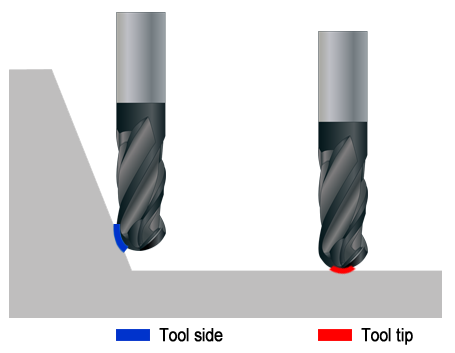
Tool tip: 2-blades. The [Feed speed] can not be increased.
Contour Face Cut Machining / High-feed Machining
The exclusive cutter paths are generated and output for “High-feed Machining” with utilizing the characteristics of the high feed milling cutter. Machining time is reduced with the best cutter paths.
Outputs tool paths are modified so that they pass through the uncut areas.Adjusts pick width in the XY.
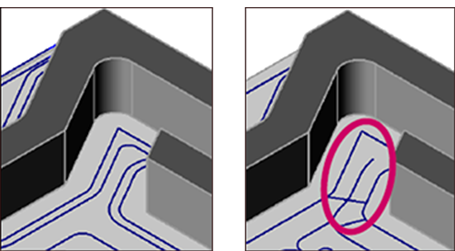
Outputs forward and return tool paths passing through the center of uncut areas.
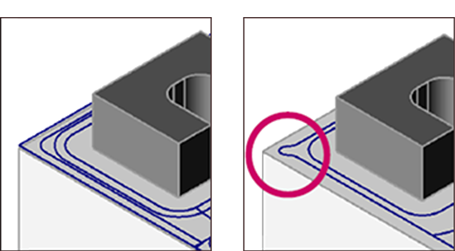
Contour Corner R / Groove Path Restriction Function
Uncut areas are determined if they are grooves and [Along-area] paths are restricted. In [Corner R Machining], the tool path of [Along-area] may be irregular at the grooves. This function solves this problem.
[CR Machining Mode/Along-area]
Tool paths are removed in the grooves.
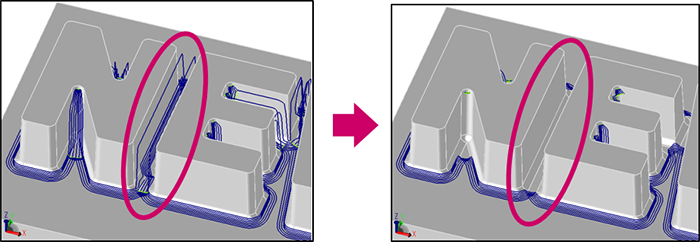
[CR Machining Mode/Contour + Along-area]
Tool paths of [Contour] are output for the entire groove.

Contour Projection Machining / Bottom Corner R
This restricts tool load at corners and prevents tool chatter during machining.
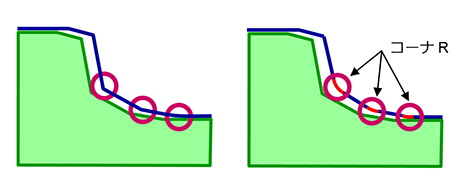
Flat Machining / Round Insert cutter Interference Check Function
When tilt infeed is performed with a round insert face mill, the function automatically adjusts the tilt angle in the area where the workpiece and tool bottom come into contact with each other, thereby preventing interference with the workpiece.
When there are narrow pockets with which the tool base interferes.
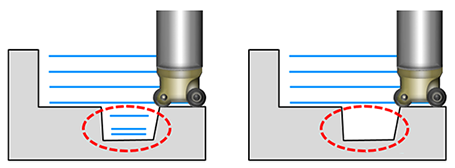
Tilt Angle at Infeed
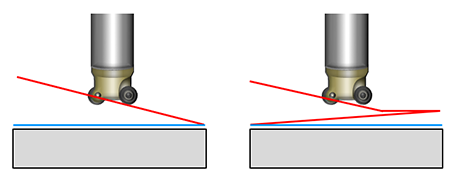
Route Machining and 2D Route Machining / Add to “zigzag” motion
The machining time can be reduced as drive-in cutting of open curves has become more efficient.
2D Route Machining
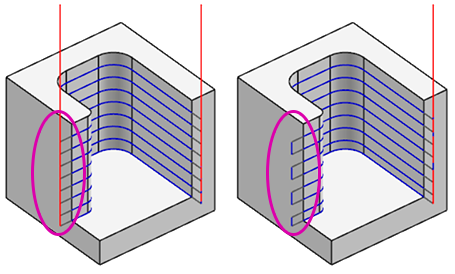
Left: One-way
Heidenhain Canned Cycle Support
Now, Heidenhain canned cycle can be used for [Drilling], [Thread Cutting], “spot face machining”, and “chamber machining”. You can define the Motion Type for cycles 200, 201, 202, 203, 204, 205.
Operation
STEP、CATIA V5 Import Layer Compatibility
If the [Translate Attributes] checkbox in [Input File Option Setting] is selected, “layer attributes” will also be converted in the same way as “color attributes”.
Addition of Machining Name Consecutive Number Renaming Function
[Machining Name] copied from the User Data Base can be changed in a batch to names which are easy to manage.
Machining Name Consecutive Number Renaming

Output File Name Consecutive Number Renaming
[Simulation] tab

Output File Name Consecutive Number Renaming
[Repost – Information] tab
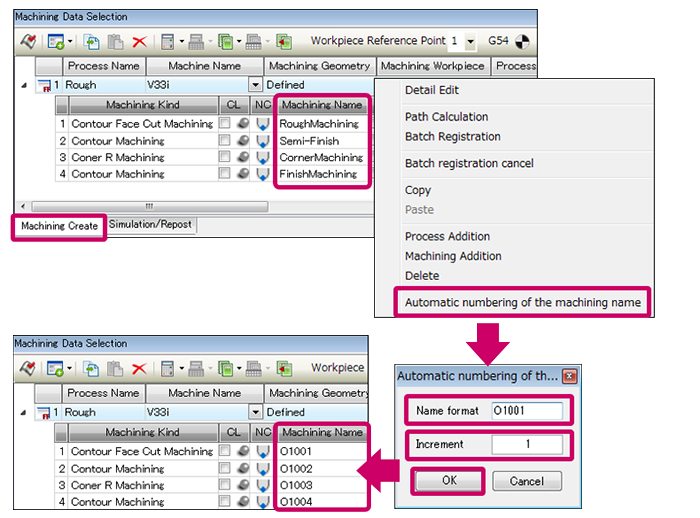
CL Editor
Improvement of CL Edit and Operability
The selection method of functions such as “Move/Copy”, “Delete CL”, and “Change Setting” of [CL Edit] has been changed to the toolbar dropdown list. Operability has improved as screen operations are simpler and more efficient.
Deletion of Block Unit Function
CL can now be selected in the units of “Z level”, “cutting”, “segment”, and “approach”. This enables the objectives of the operators to be reflected more easily. Operation mistakes can also be prevented by limiting the CL entities to be deleted.