FFCAM 2019 New Function
Machining Function
Removed Restriction on Lens Barrel Tool
Contour Face Cut
This function allows you to perform rough and finish machining of contour using lens barrel tools.
Stock Support(read and save)
This function allows you to accurately identify the uncut portions after using lens barrel tools and create machining without waste in the next process.
Add of Function to Specify the Progress Direction for Tool Path
A function has been added to obtain the progress direction for the tool path from the geometry when “One-way” or “Zigzag” is selected for scan motion or contour face cut motion.
For index machining function, even in the case of machining where the angle of the scan motion is unclear, you can now set the progress direction without measuring or by trial and error.
The following machining types can be set.
- Projection Machining
- Specify Projection Direction of Contour Projection Machining
- Flat Face Machining
- Contour Face Cut Machining
Results of setting zigzag motion in the X-axis direction using the previous function
The tool path is output in the X-axis direction after index setting.
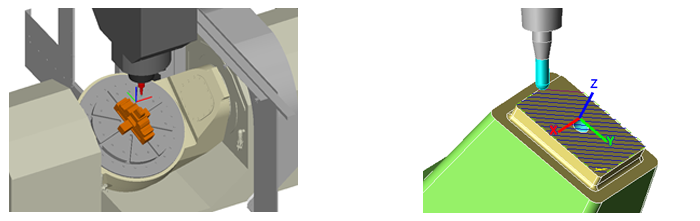
When using “Function to Specify the Progress Direction for Tool Path”
In [Path Direction Setting] (Example:2 Points), specify the edge of the blue arrow.
The tool path is output in the X-axis direction before the index setting.
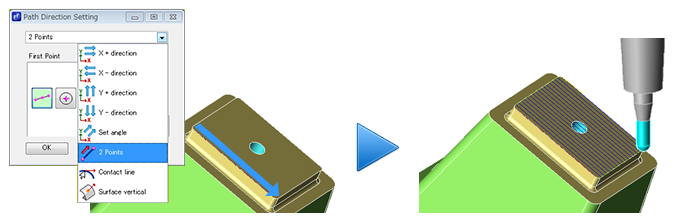
Add of Common Machining Start Point Setting for Drilling
Since the start/end point of multiple drilling points can be defined together, the work time can be reduced, and rework due to missing the settings can be eliminated.
Add of Function to Obtain Pre Machining Information
The setting values of the pre-machining tool and finishing allowance of pre-machining for Corner R Machining and Contour Machining (when [Tool Load Priority] is specified in the machining order) can now be obtained from the pre-machining.
The value set in the pre-machining can be obtained by just clicking the [Acquisition of Pre-machining tool/Finishing allowance] button.
Even if you forget the pre-machining information, you can set the pre-machining information without returning to pre-machining screen for confirmation.
Add of Machining Direction Setting Function Independent of Machine Configuration
In index machining of FFCAM, the machining direction is set by directly entering the angle for the machine rotation axis. However, in the case of machines where the rotation axis is not parallel to the X/Y/Z axis, setting the required angle was sometimes difficult.
In FFCAM 2019, a function to set an angle based on X/Y/Z axis has been added.
You can set an angle regardless of the machine axis configuration.
Operation
Add of Function to Open the Location for Saving FFCAM Data
You can now open the folder where the file used at present is saved with one click.
You can easily access the required folder.
Add of Function to View Files as Thumbnails
The saved FFCAM file (.xMtn) is now displayed with a thumbnail of the geometry image in Windows Explorer.
Since the model geometry can be confirmed without opening the file, making file selection easier.
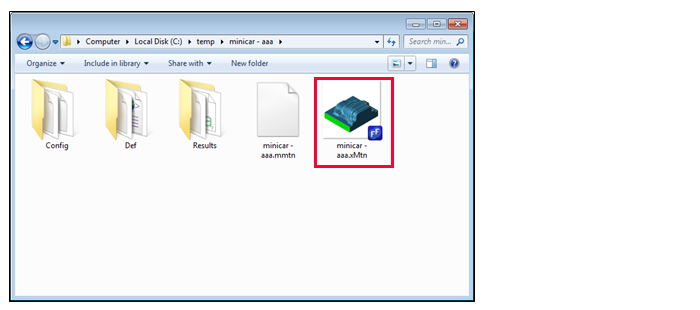
Add of Comment Display Function for Files
Comments can now be added to FFCAM files (.xMtn).
The comments that are added can be viewed and checked in Windows Explorer.
Using it together with the Function to View Files as Thumbnails of the previous chapter makes file selection in FFCAM easier.
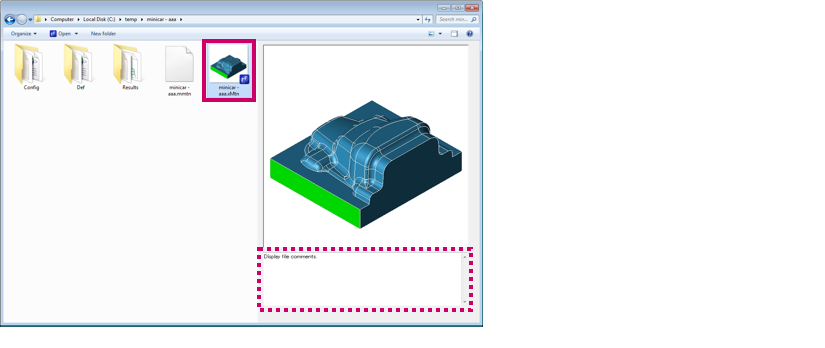
Add of Comment Display Function for Process
Comments can now be added to processes.
You can record and convey the details and production intention of the machining that has been created by entering the explanation for the machining, and matters to be handed over.
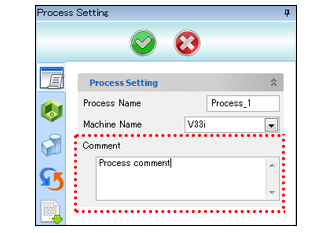
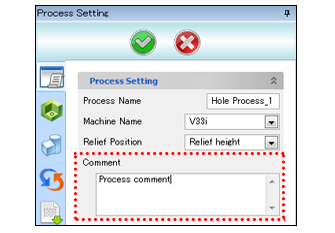
Machining Preparation Wizard
Add of Function to Set the Hole to the Center of Geometry Direction
You can align the direction of the selected hole to the center direction of the geometry.
You can set from the selection list of the Hole Machining Data Creation → [Hole Position].
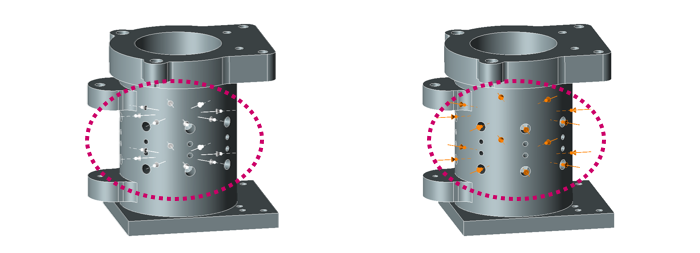
Add of Function to Set the Direction of Hole to the Specified Point
You can align the direction of the selected hole to the specified direction.
You can set from the selection list of the Hole Machining Data Creation → [Hole Position].
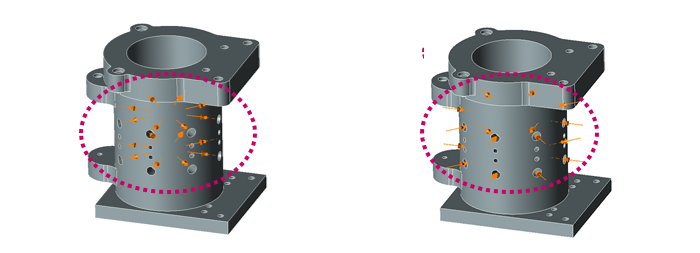
Add of Surface Filter Function
When selecting a hole to be machined, only holes on the selected surface can be registered.
You can set from the selection list of the Hole Machining Data Creation → [Hole Position].
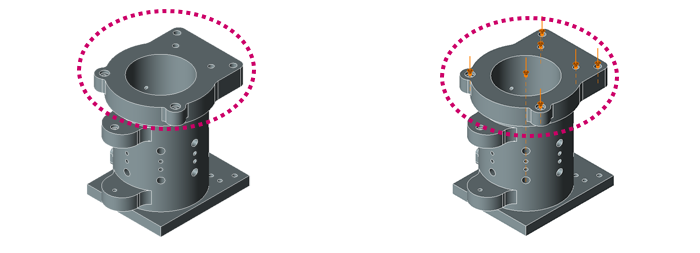
Option
[5-Axis Dedicated Simultaneous Machining] Add of Function to Specify Tool Contact Points
In 5-axis dedicated simultaneous (Parallel, Along Surface, Route) machining, the portion where the tool touches the machining work can be now specified.
When using flat end mill and bullnose end mill tools, you can specify the part of the tool to be used such as “Corner” and “Bottom face”.
Tool Contact Point

Auto (Default)
The contact position between the tool and drive surface is determined automatically according to the tilt of the tool.
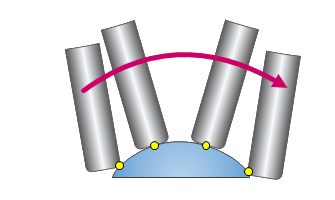
Tip
The tool position is set so that the tool tip center touches the drive surface.
A collision may occur between the tool and workpiece depending on the geometries of the tool and drive surface.
Therefore, use this parameter with [Avoid tool collision] enabled.
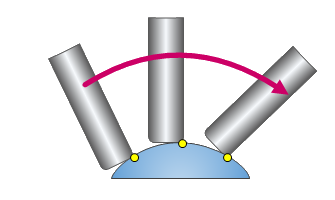
Front
The tool posture is set so that the front blade touches the drive surface to the progress direction of the tool.
A collision may occur between the tool and workpiece depending on the geometries of the tool and drive surface.
Therefore, use this parameter with [Avoid tool collision] enabled.
[Machine Simulator] Addition of Detail Parameter for “Ignored Code”
Due to the G and M codes that are not supported by Machine Simulator, unexpected operations may be performed during simulation.
In the new Machine Simulator, you can specify code that is not executed for simulation (Ignored Code) to avoid such unexpected operations.
Codes registered as ignored code are read as NC program but do not operate during the simulation.
[Machine Simulator] Enhancement of Call Level of Logs
“Information” has been added to the call level of logs of the Machine Simulator.
Previous “Warning” and “Alarm” of call level were linked with the function to pause the simulation.
“Information” logs only information without pausing the simulation.
You can record the phenomenon of stopping and confirming the simulation and the phenomenon of logging only information without stopping the simulation.
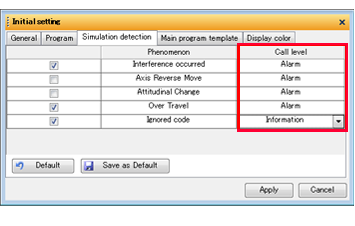